Home > Wat Application Guide
Intended Use:
Key to Proper Activation: WATER
Ideal Water Temperature = 110°F
The recommended water temperature for activation is 110°F. While colder water can be used, it will slow down adhesive activation and extend the open time. Conversely, warmer water (above 110°F) will speed up activation, causing the adhesive to set more quickly. However, using warmer water is not advised in practice, as it can lead to excessive adhesive buildup on the brushes of tape machines, requiring more frequent cleaning or replacement.
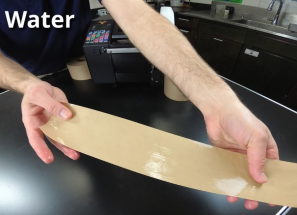
Most Common Mistake: Maxing Out the Brush Heater
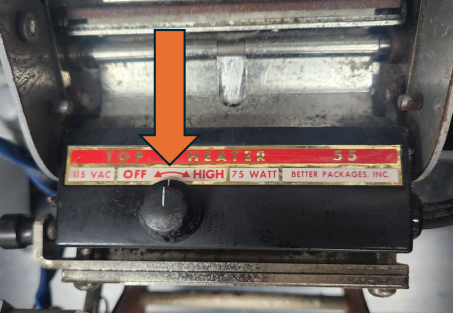
Brushes – Why they are so important?
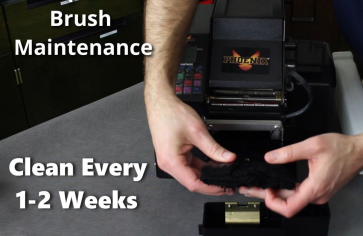
Applying water to the tape works on the same principle as painting a wall in your home. Imagine trying to paint with a crusty, old brush—how would that turn out?
The same logic applies to the brush in a water activated tape dispenser. The condition and cleanliness of the brush are crucial for proper application.
A clean, well-maintained brush ensures an even and properly metered application of water to the tape. Poor brush condition and uneven water distribution are the most common issues when using water-activated tape. The good news? It’s an easy fix—just clean the brush!
Soaking the brush in hot water for 10–15 minutes helps dissolve adhesive residue. Agitate the brush to flush out the build-up adhesive
and rinse thoroughly.
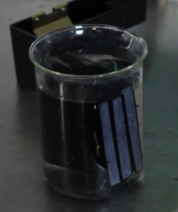
Proper Dispensing
To ensure consistent application of water activated tape, a high-quality tape dispenser is essential. Holland recommends the Phoenix line of tape dispensers for their durable, metal sideframe construction and reliable performance. Both manual and electric models are available,
but Holland advises using an electric dispenser equipped with a brush heater for optimal results.

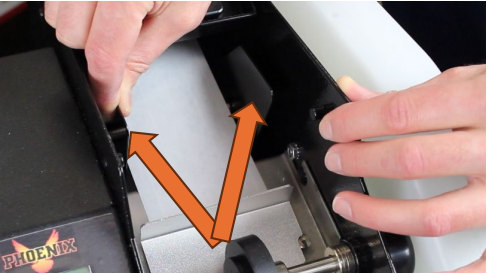
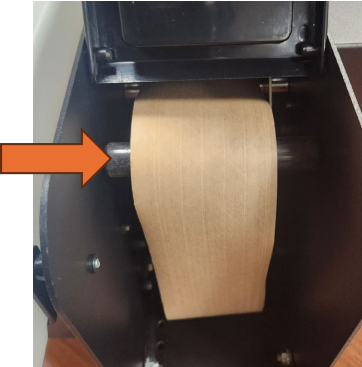
The tape path inside the tape machine is critical for proper dispensing. In most tape machines, there are rollers that guide the tape from the tape roll to the dispensing point. The tape must be threaded over the top of these rollers.
Pay attention to the metal side guides, which control the lateral movement of the tape roll. These guides are especially important when using larger rolls, such as 600’ or 1000’ rolls.
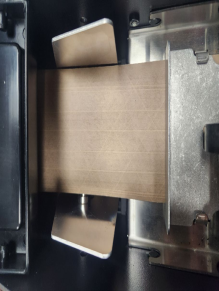
Setting the Correct Water Level
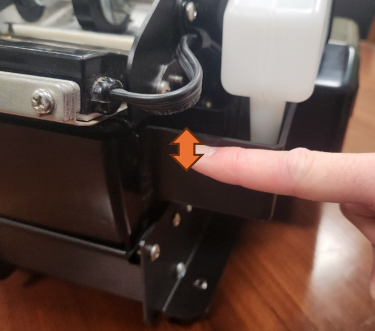
The proper water level is approximately ½” or 1 finger width from the top of the brush reservoir. This level of water will provide an accurate amount of water to the brush for application to the tape.
To adjust the water level, use the white plastic screw located at the water bottle’s interface with the brush reservoir. Turning the screw outward increases the water level by raising the height of
the interface, while turning it inward lowers the water level.
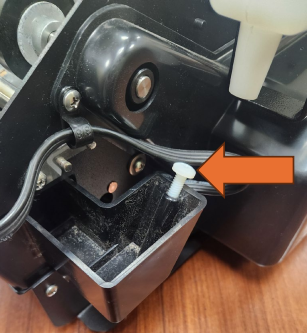
Applying the Tape to the Box
Applying pressure is crucial as it helps embed the adhesive into the corrugated surface, enhancing the
mechanical bond between the adhesive and the corrugated material.
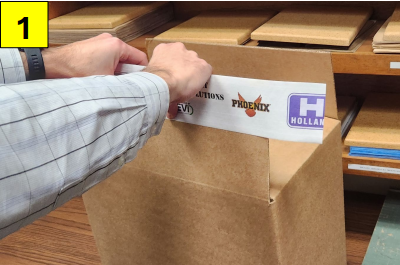
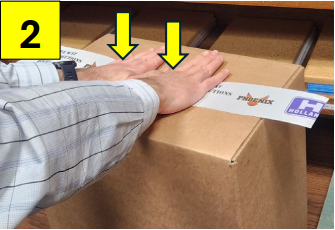
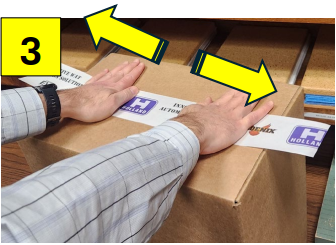
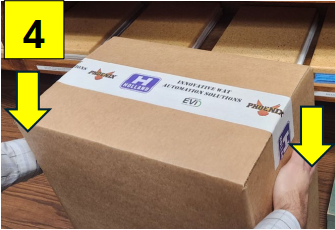
Holland recommends a minimum 3” of tape length down the side of the minor panel of the box. Most water activated tape dispensers have inch length selections – select a length 6” longer than the major panel length and dispense.
Correct Length = BOX LENGTH + 6”
H-Seal for Additional Security
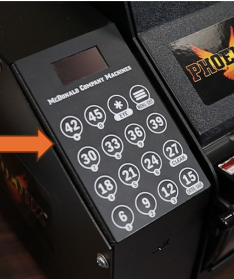
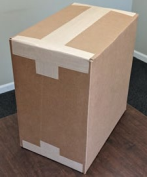
Troubleshooting Tips
- Problem: Tape is not sticking
- Is the adhesive fully activated and fluid across the tape’s entire width?
If not:
- Check the water level in the reservoir.
- Agitate the brush to ensure water reaches the tape effectively.
- Clean or replace the machine brush if needed.
Ensure the brush heater is functioning properly and not obstructed. Obstructions reduce hold-down pressure at the water application interface, significantly decreasing water distribution.
2. Is the tape being applied to a corrugated or paper-based substrate?
- Water-activated tape is designed exclusively for fiber-based surfaces. It will not adhere to non-fiber substrates.
3. What is the water temperature in the tape machine?
- Replace the water in the reservoir with fresh water heated to the recommended 110°F for optimal adhesive activation.
4. Are you switching between tapes from different manufacturers?
- Different manufacturers use unique adhesive formulations, and their chemistries may interfere with one another
- When switching tape brands, completely replace the water in the reservoir and brush tray. Additionally, thoroughly clean the brushes to avoid cross-contamination.
Problem: Tape is jamming in the tape machine
- Improper Control of Tape Unwinding
- Ensure the tape guides at the rear of the tape machine are correctly positioned within ½ inch of the tape’s width.
- Verify that the tape is following the proper web path as specified by the tape machine manufacturer.
2. Tape Not Cutting Cleanly
- If the tape does not cut cleanly, inspect the shear blade. A worn blade may need to be replaced to restore proper cutting performance.
3. Tape Guide Plate Missing Before the Shear Cutter
- Ensure the metal guide plate located before the shear
cutter is installed correctly. This plate is essential for guiding the tape accurately through the cutting mechanism, preventing misalignment and ensuring clean cuts.
4. Obstruction in the Shear Cutter
- Clean any debris or material stuck in the shear cutter. Use a puddy knife and keep hands clear of the shear when exercising to clear area.